Introduction
Rotary optical encoders are precision devices that convert rotational movement into digital signals. Used in everything from industrial robots to your computer mouse, these components offer unmatched accuracy for position and speed detection.
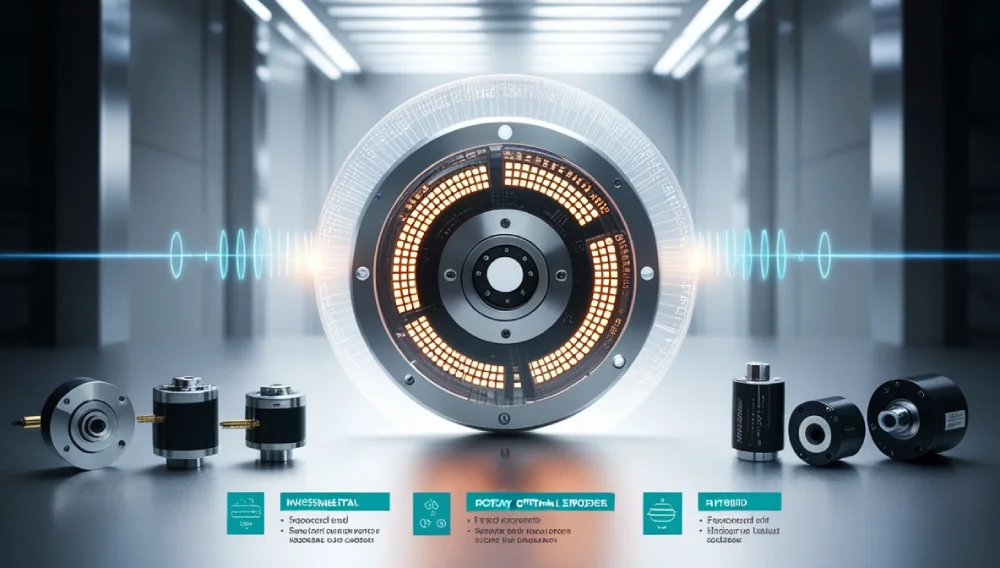
Amazon Featured
Amazon Newest Arrivals
Key applications include:
- CNC machines
- 3D printers
- Medical equipment
- Automotive systems
- Consumer electronics
How Optical Rotary Encoders Work
Basic Working Principle
- A light source (usually LED) shines through a coded disk
- The disk has precise transparent/opaque patterns
- Photodetectors read the light patterns
- Electronics convert this into digital position data
Key Components
- Code disk: Glass or plastic with radial pattern
- Light emitter: Typically infrared LED
- Photodetector array: Reads light pulses
- Signal processor: Converts to digital output
Types
1. Incremental Encoders
✔ Outputs pulse trains (A/B signals)
✔ Requires homing for position reference
✔ Best for speed measurement
2. Absolute Encoders
✔ Provides unique position code
✔ Maintains position after power loss
✔ Essential for critical positioning
3. Hybrid Encoders
✔ Combines incremental and absolute
✔ Offers both high-speed and position data
✔ More expensive but versatile
Top 5
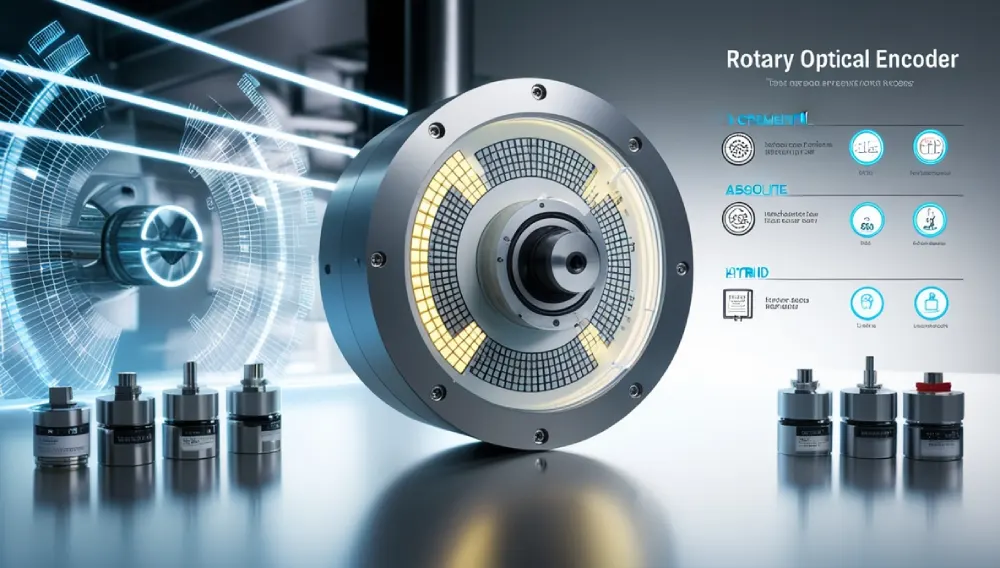
1. Omron E6B2-CWZ6C
✔ Pros:
- 2000 PPR resolution
- IP50 protection
- Reliable industrial performance
✔ Cons: - Not waterproof
- Sensitive to misalignment
Best for: Factory automation
2. US Digital E5
✔ Pros:
- Affordable pricing
- 100-5000 CPR options
- Easy microcontroller interface
✔ Cons: - Basic environmental sealing
- Limited to TTL output
Best for: Hobbyists and education
3. Renishaw RESOLUTE
✔ Pros:
- Ultra-high resolution (up to 1nm)
- Absolute position data
- Robust industrial design
✔ Cons: - Very expensive
- Complex installation
Best for: Precision CNC and metrology
4. Autonics E40H
✔ Pros:
- Compact size
- 100-5000 PPR options
- Cost-effective
✔ Cons: - No absolute option
- Basic protection only
Best for: Small machinery
5. Heidenhain ROD 426
✔ Pros:
- Industrial-grade durability
- High resolution options
- Multiple interface options
✔ Cons: - Premium price
- Requires expertise to install
Best for: High-end manufacturing
Key Specifications Explained
Resolution (PPR/CPR)
- Pulses/Counts per Revolution
- Higher numbers = finer position control
- Typical range: 100-10,000 PPR
Accuracy vs. Resolution
- Resolution: Smallest detectable movement
- Accuracy: How close to true position
Output Types
- TTL: 5V digital (common for microcontrollers)
- HTL: 10-30V (industrial PLCs)
- SSI/RS422: For long-distance signals
Environmental Ratings
- IP54: Dust protected
- IP67: Waterproof
- Operating temperature range
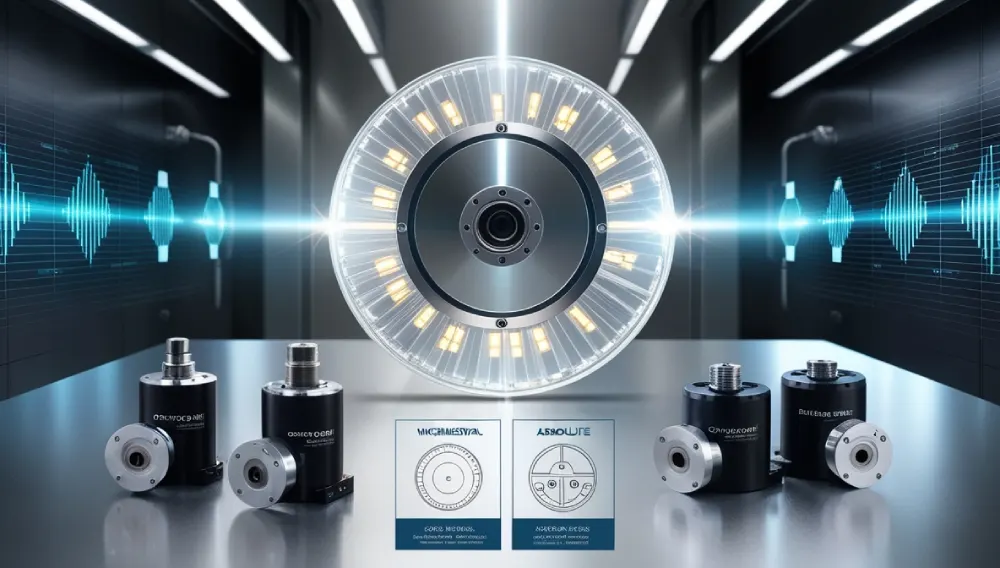
Buying Guide
1. Determine Your Needs
- Basic position sensing: 100-500 PPR
- Precision control: 1000-5000 PPR
- Ultra-high precision: 5000+ PPR
2. Select the Right Type
- Speed measurement: Incremental
- Position critical: Absolute
- Budget projects: Basic incremental
3. Consider Mechanical Fit
- Shaft size (6mm, 10mm common)
- Through-bore vs. solid shaft
- Mounting flange type
4. Environmental Factors
- Clean lab vs. dirty factory?
- Temperature extremes?
- Vibration exposure?
5. Interface Requirements
- Microcontroller (TTL)
- Industrial PLC (HTL)
- Long cable runs (RS422)
Installation Best Practices
Do’s
✔ Use proper shaft couplings
✔ Align precisely to avoid eccentricity
✔ Secure cables with strain relief
✔ Keep within specified RPM limits
Don’ts
✖ Exceed maximum radial/axial load
✖ Bend cables sharply
✖ Ignore environmental limits
✖ Use in condensing environments without protection
Troubleshooting Common Issues
Problem: Erratic Signals
- Causes: Misalignment, dirty disk, electrical noise
- Fix: Realign, clean with alcohol, add ferrite beads
Problem: No Signal Output
- Causes: Dead LED, wiring fault, power issue
- Fix: Check voltage, inspect connections
Problem: Inconsistent Counts
- Causes: Vibration, mechanical play
- Fix: Secure mounting, check bearings
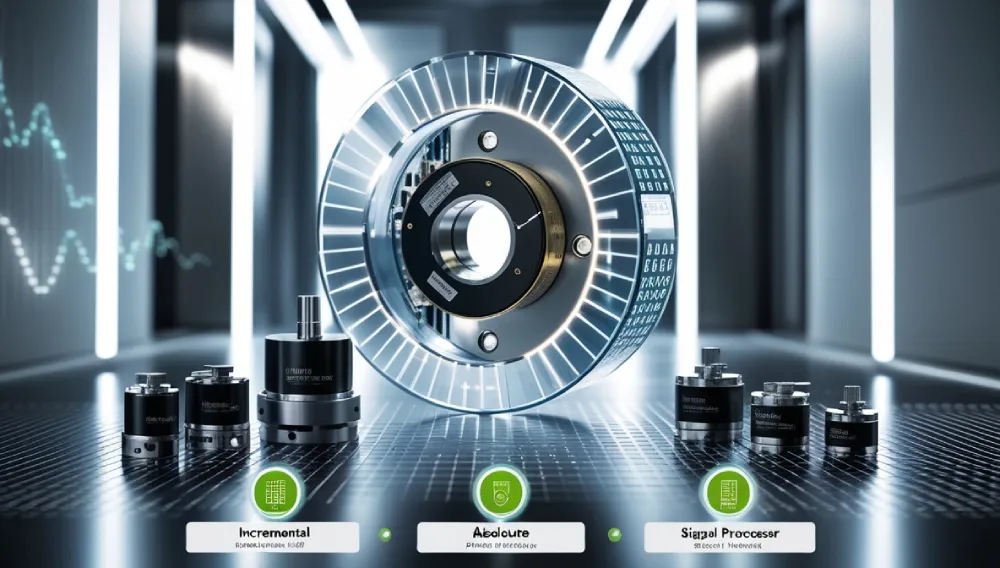
Personal Experience: CNC Retrofit Story
When upgrading my CNC mill, I chose a Renishaw absolute encoder for the spindle. The difference was incredible:
- Position accuracy improved by 5x
- No more homing routines after power cycles
- Consistent performance despite coolant spray
The investment paid off in better part quality and less downtime.
For my 3D printer project, a US Digital E5 provided excellent value – the 1000 CPR resolution was perfect for bed leveling.
FAQs
Q: How long do optical encoders typically last?
A: 50,000+ hours for quality models – the LED is usually the first point of failure.
Q: Can I clean an optical encoder?
A: Yes, with isopropyl alcohol and lint-free swabs – avoid scratching the disk.
Q: Why choose optical over magnetic?
A: Optical offers higher resolution and better accuracy in clean environments.
Q: What’s the difference between PPR and CPR?
A: PPR = physical pulses, CPR = counts after electronic interpolation.
Q: Can optical encoders get wet?
A: Only IP67+ rated models – most are damaged by moisture.
Future Trends in Encoder Technology
Emerging developments to watch:
- Miniaturization: Smaller high-resolution models
- Smart encoders: Built-in diagnostics
- Wireless options: For rotating applications
- Improved durability: Better contamination resistance
Final Recommendations
For industrial use: Omron or Heidenhain offer the best reliability
For precision needs: Renishaw is the gold standard
For makers/hobbyists: US Digital provides great value
Remember to match your encoder to your specific requirements for resolution, environment, and interface needs.
Have questions about choosing a rotary optical encoder? Ask in the comments below!
Read More: sdi iptv encoder
1 thought on “The Best Rotary Optical Encoder”