If you’re diving into the world of encoders, you’ve likely come across the term “absolute encoder.” But what exactly is it, and why is it so important? In this article, we’ll break down everything you need to know about encoders, from their basic functionality to their applications, and even provide some product recommendations. Whether you’re a beginner or a seasoned professional, this guide will help you understand and choose the right encoder for your needs.
What is an Absolute?
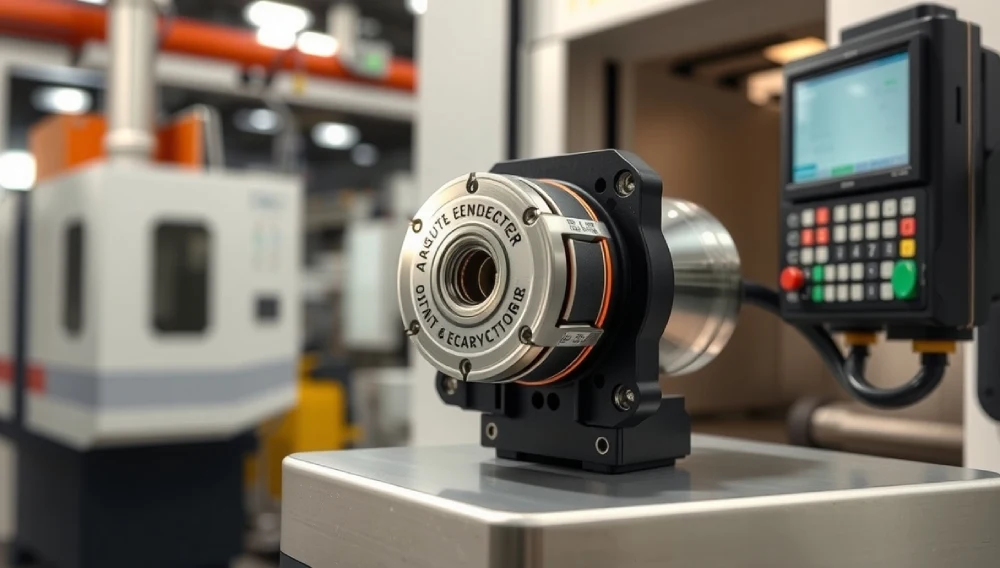
Amazon Newest Arrivals $ 257.10
An absolute is a device that converts the angular position or motion of a shaft into a digital signal. Unlike incremental encoders, which only provide relative position information, encoders give a unique digital code for each position, even after a power loss. This makes them incredibly reliable for applications where precise positioning is crucial.
Key Features
- Unique Position Identification: Each position has a unique code.
- Power Loss Resilience: Retains position data even after power loss.
- High Precision: Offers accurate position feedback.
- Versatility: Available in single-turn and multi-turn configurations.
How Does an Absolute-Encoder Work?
Encoders use a variety of technologies to achieve their high precision and reliability. The most common types include optical, magnetic, and capacitive encoders.
Optical
- How They Work: Use a light source and a photodetector to read a coded disc.
- Pros: High resolution and accuracy.
- Cons: Sensitive to dust and debris.
Magnetic
- How They Work: Use magnetic fields to detect position changes.
- Pros: Durable and resistant to environmental factors.
- Cons: Generally lower resolution compared to optical encoders.
Capacitive
- How They Work: Changes in capacitance are used to determine position.
- Pros: High resolution and durability.
- Cons: Can be more expensive.
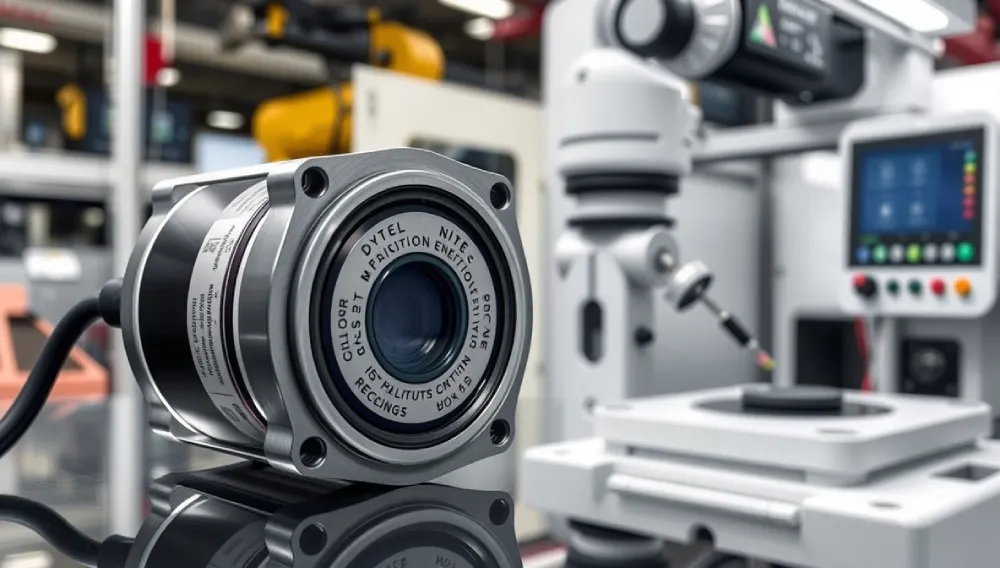
Enhance Accuracy with Rotary Encoder Solutions
Applications
Absolute encoders are used in a wide range of industries and applications. Here are some common uses:
- Industrial Automation: For precise control of machinery and robots.
- CNC Machines: To ensure accurate positioning of tools.
- Medical Devices: For precise movement in surgical robots and imaging systems.
- Aerospace: In-flight control systems and satellite positioning.
- Renewable Energy: For tracking the position of solar panels and wind turbines.
Measure Angles with Absolute Accuracy – Learn More
Product Recommendations
Choosing the right absolute encoder can be challenging, especially with so many options available. Here are a few top picks to consider:
1. Omron E6CP-A Encoder
- Pros: High resolution, durable, easy to install.
- Cons: Slightly higher price point.
- Best For: Industrial automation and CNC machines.
2. Broadcom AEAT-8800 Magnetic Encoder
- Pros: High durability, and resistance to environmental factors.
- Cons: Lower resolution compared to optical encoders.
- Best For: Harsh environments and outdoor applications.
3. Heidenhain RON 786 Absolute
- Pros: Exceptional accuracy, robust construction.
- Cons: Expensive.
- Best For: High-precision applications like medical devices and aerospace.
Unlock Perfect Angle Measurement Today
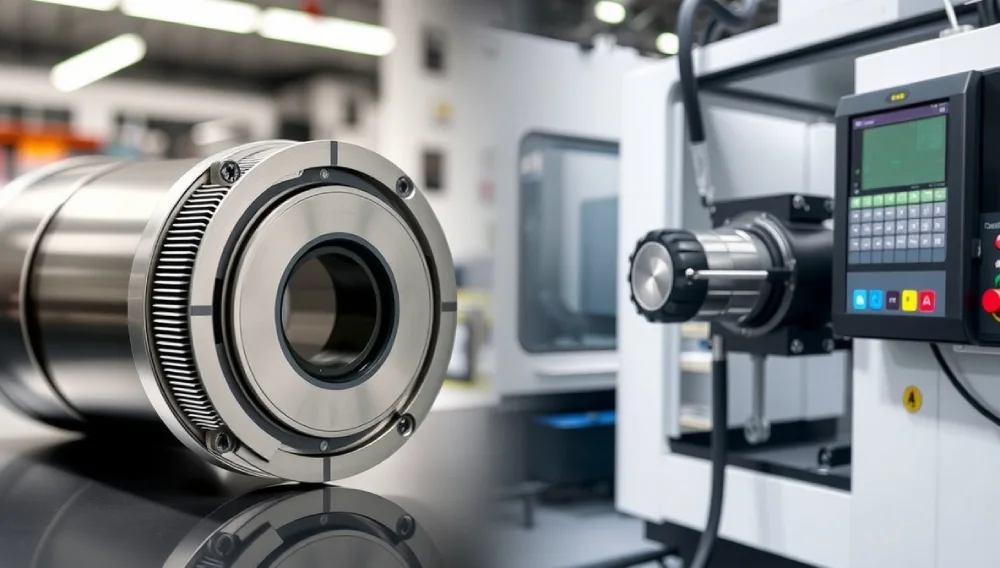
Buying Guide
When selecting an encoder, consider the following factors:
1. Resolution
- What It Means: The number of unique positions per revolution.
- Why It Matters: Higher resolution provides more precise position feedback.
2. Durability
- What It Means: The encoder’s ability to withstand environmental factors like dust, moisture, and temperature.
- Why It Matters: Ensures long-term reliability, especially in harsh conditions.
3. Interface
- What It Means: The type of output signal (e.g., SSI, SPI, CANopen).
- Why It Matters: Compatibility with your existing system.
4. Single-Turn vs. Multi-Turn
- What It Means: Single-turn encoders measure position within one revolution, while multi-turn encoders can track multiple revolutions.
- Why It Matters: Multi-turn encoders are essential for applications requiring position tracking over multiple rotations.
5. Price
- What It Means: The cost of the encoder.
- Why It Matters: Balance between budget and required features.
Personal Experience
In my experience, encoders have been a game-changer in projects requiring high precision and reliability. For instance, in a recent CNC machine upgrade, switching to an absolute encoder significantly improved the machine’s accuracy and reduced downtime caused by position errors. The initial investment was higher, but the long-term benefits far outweighed the costs.
Shaft Encoders for Industrial Precision – Get Yours Now

FAQs
1. What is the difference between an absolute and an incremental encoder?
- Encoder: Provides a unique digital code for each position, even after power loss.
- Incremental Encoder: Provides relative position information and requires a reference point.
2. Can absolute encoders be used in harsh environments?
Yes, especially magnetic encoders, which are designed to withstand harsh conditions.
3. How do I know if I need a single-turn or multi-turn absolute?
- Single-Turn: Suitable for applications where the shaft rotates less than 360 degrees.
- Multi-Turn: Necessary for applications requiring position tracking over multiple rotations.
4. Expensive?
They can be more expensive than incremental encoders, but the investment is often justified by their reliability and precision.
5. Can I replace an incremental encoder with an absolute?
Yes, but you may need to update your control system to accommodate the different output signals.
Conclusion
Absolute is indispensable in applications requiring precise and reliable position feedback. Whether you’re working in industrial automation, medical devices, or renewable energy, understanding the different types and features of absolute encoders can help you make an informed decision. By considering factors like resolution, durability, and interface, you can choose the right encoder for your needs. And with top product recommendations like the Omron E6CP-A and Heidenhain RON 786, you’re well on your way to enhancing your system’s performance.
More
Explore Magnetic Accuracy with Hall Effect Encoders
Why Mechanical Encoders Still Matter
Pinpoint Accuracy with Angle Encoders
1 thought on “The Best Absolute Encoder”