Introduction
When it comes to controlling motion with precision, BLDC servo motors have become a leading choice in modern automation. Whether you’re working on robotics, CNC machinery, or any high-performance industrial application, these motors offer unparalleled precision, energy efficiency, and durability. Simply put, a BLDC servo motor combines the advantages of brushless DC motors with sophisticated servo control to deliver smooth, accurate motion.
In this article, we will explain what a BLDC servo motor is, how it works, its key components and features, and the benefits it offers. We’ll also cover practical applications, factors to consider when choosing one, and maintenance tips to ensure long-term performance.
What is a BLDC Servo Motor?
A BLDC (Brushless DC) servo motor is an electric motor known for its high efficiency and precise control. Unlike traditional brushed motors, BLDC motors do not have brushes that wear out over time. Instead, they use electronic commutation, which not only increases the lifespan of the motor but also improves its performance. When combined with a servo control system, BLDC motors can be used for applications that require very accurate positioning, speed control, and dynamic adjustment.
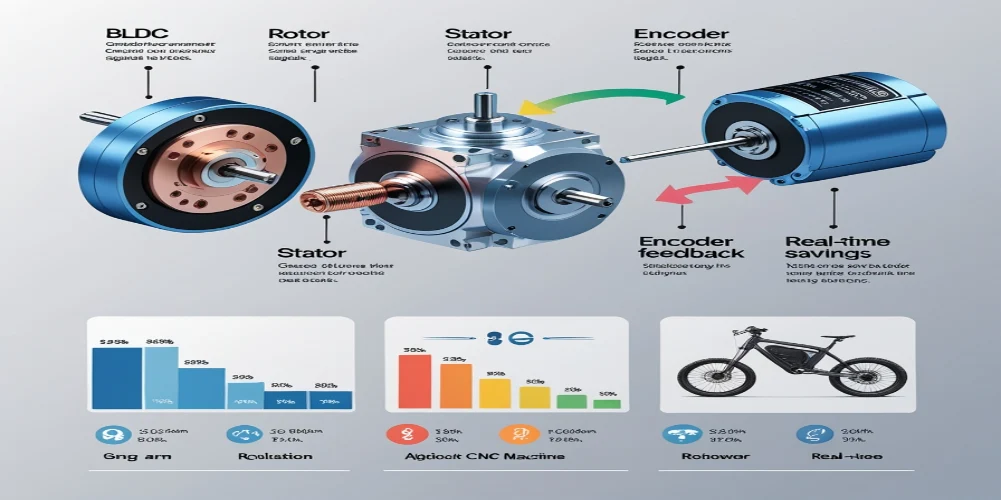
Key Features
- Zero Brushes, Zero Fuss: No brushes mean less wear, lower maintenance, and a lifespan that outlasts brushed motors.
- Pinpoint Accuracy: Built-in encoders or Hall sensors provide real-time feedback, ensuring movements stay on target.
- Energy Saver: Converts 85-90% of electrical energy into motion (brushed motors: 75-80%).
- Whisper-Quiet: Perfect for hospitals, labs, or your living room.
How Does a BLDC Servo Motor Work?
Let’s simplify the tech magic:
Core Components
- Brushless DC Motor:
- Rotor: Packed with permanent magnets.
- Stator: Copper windings create magnetic fields.
- No brushes! Electronic signals control rotation.
- Sensors:
- Encoders or Hall sensors track position/speed.
- Controller:
- The “brain” that adjusts power based on sensor feedback.
- Power Supply:
- Fuels the motor, often optimized for efficiency.
Working Principle
- Electronic Commutation:
- The controller sends signals to the stator, creating a rotating magnetic field that spins the rotor.
- Feedback Loop:
- Sensors constantly report the motor’s status. Too slow? The controller ramps up power. Off-track? It corrects instantly.
- Real-Time Adjustments:
- Adapts to load changes in milliseconds—ideal for sudden stops or speed shifts.
Top 5 Benefits of BLDC Servo Motors
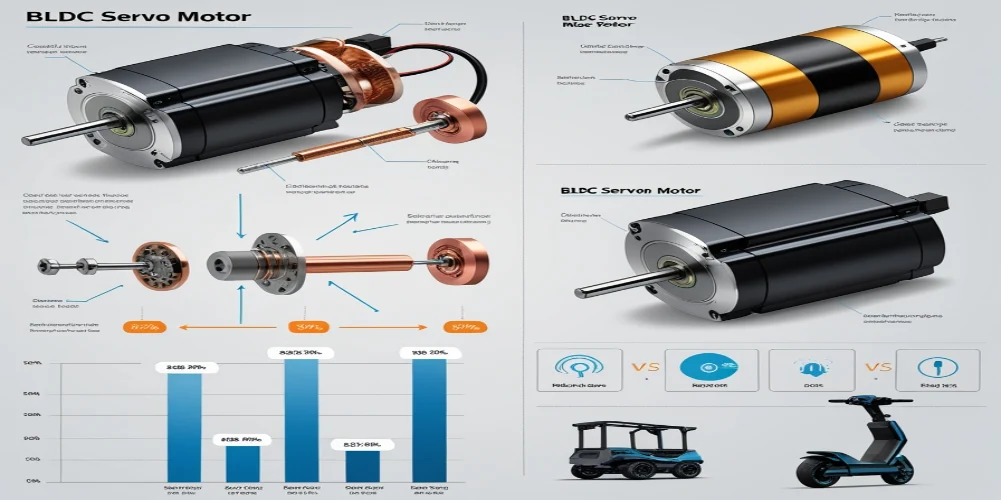
- Energy Efficiency
- Save 15-20% on power bills vs. brushed motors.
- Example: A factory cutting energy costs by upgrading conveyor belts to BLDC motors.
- Surgical Precision
- Achieve tolerances as tight as 0.01mm (think laser engraving or robotic surgery).
- Built to Last
- No brushes = 2-3x longer lifespan. Perfect for 24/7 operations.
- Silent Operator
- Runs quieter than a library whisper—ideal for MRI machines or drones.
- Versatility
- Scale from tiny drone rotors to massive industrial presses.
Where Are BLDC Servo Motors Used?
Industry | Application | Why BLDC? |
Industrial | CNC machines, robotic arms | Precision cutting, 24/7 reliability |
Medical | Surgical robots, MRI systems | Quiet, vibration-free operation |
Aerospace | Drone propellers, satellite actuators | Lightweight, high torque |
Consumer Tech | Camera gimbals, electric scooters | Smooth motion, long battery life |
Automotive | Electric power steering, EV cooling | Efficiency, rapid response |
How to Choose the Right BLDC Servo Motor: 6-Step Checklist
- Torque & Speed
- Need to lift heavy loads? Prioritize torque. For rapid spins, focus on RPM.
- Voltage Match
- Ensure your power supply aligns with the motor’s specs (e.g., 24V or 48V).
- Size Matters
- Measure your space! A 50mm motor might not fit a drone designed for 30mm.
- Feedback Quality
- Optical encoders > Hall sensors for precision tasks like 3D printing.
- Environment Proofing
- For dusty factories or outdoor use, pick IP65-rated motors.
- Budget vs. ROI
- BLDC motors cost 20-30% more upfront but save 40%+ in energy/maintenance.
Installation & Maintenance Tips
Setup Like a Pro
- Mounting: Use anti-vibration pads to reduce noise.
- Wiring: Follow color codes—red (power), black (ground), green (signal).
- Test Run: Start at 10% load to spot issues early.
Keep It Running Smoothly
- Monthly Checks: Inspect cables for fraying.
- Dust Busting: Clean vents with compressed air.
- Software Updates: Upgrade controller firmware annually.
FAQs: Your Questions, Answered
Longer life, less noise, and better efficiency. Brushed motors wear out faster and waste energy as heat.
Yes! Many factories upgrade conveyor systems with BLDC motors for instant energy savings.
Check for blocked vents, overloading, or incorrect voltage. Let it cool and test at lower loads.
Only if rated IP67 or higher. Most are for dry/indoor use.
Skipping the encoder calibration. Always fine-tune sensors post-installation!
Conclusion: Power Your Future with BLDC Servo Motors
From factory floors to your pocket-sized gadgets, BLDC servo motors are the silent workhorses driving precision and efficiency. Whether you’re building the next Mars rover or a DIY CNC machine, choosing the right motor can make or break your project.
1 thought on “BLDC Servo Motor | Guide | Efficiency”