Picture your favorite robot gracefully moving its arms, a drone adjusting its propellers mid-flight, or a 3D printer crafting intricate designs. Behind these smooth motions is a servo motors—and its unsung hero, the motor driver for servo motor. Think of this driver as the “translator” between your robot’s brain (a microcontroller) and its muscles (the servo). Without it, your servo motor would be like a car without a steering wheel: powerful but directionless!
Whether you’re an engineer designing industrial machinery, a hobbyist building a robot, or a student tinkering with automation, this guide will explain everything you need to know about servo motor drivers. Let’s dive in!
What is a Servo Motor?
A servo motor is a smart motor that rotates to a specific angle, speed, or position based on commands. It’s widely used in:
- Robotics (robot joints, grippers).
- RC cars and drones (steering, throttle control).
- Industrial machines (conveyor belts, CNC machines).
How It Works:
- Input Signal: Receives a pulse-width modulation (PWM) signal (like a coded message).
- Internal Circuitry: Decodes the signal to determine the target position.
- Movement: Moves the motor shaft to the desired angle.
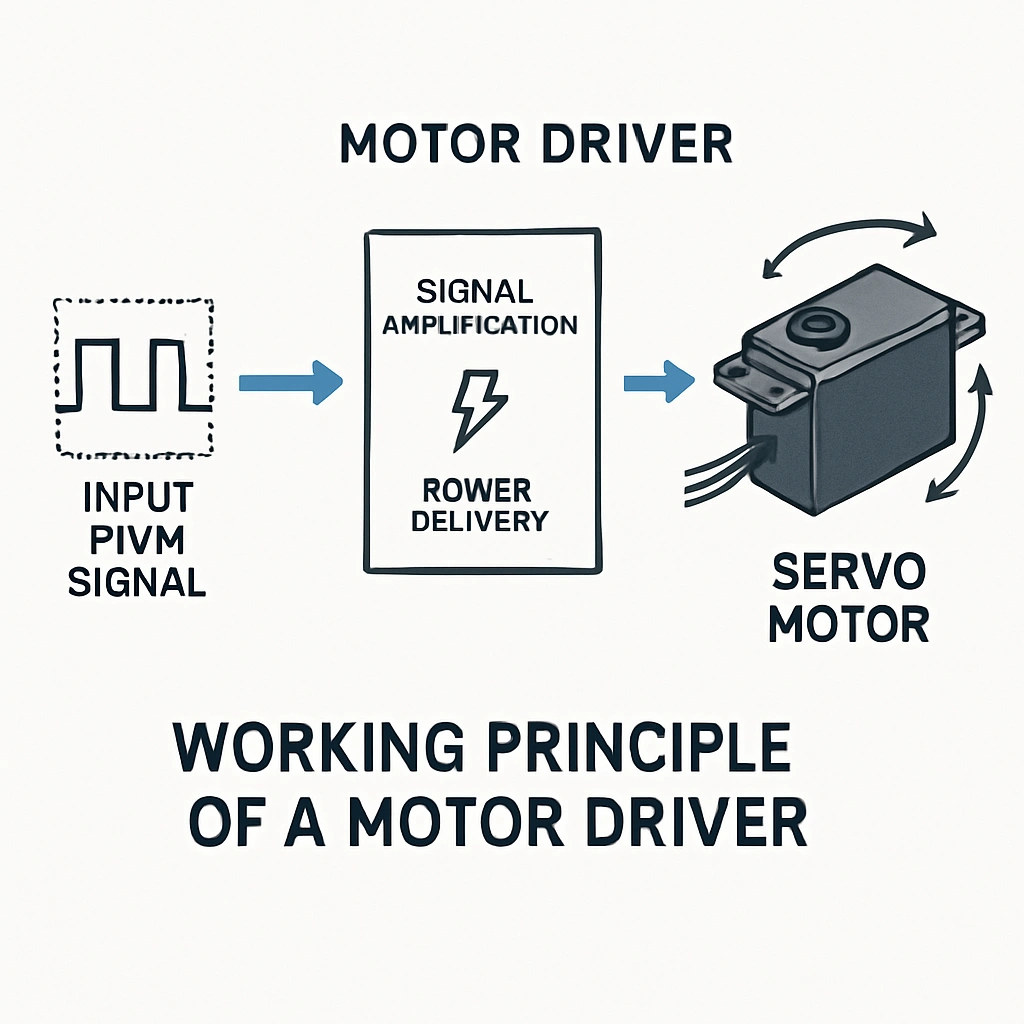
What is a Motor Driver?
A motor driver (or servo motor controller) is an electronic circuit that acts as a middleman between your control system (e.g., Arduino) and the servo motor. Its main jobs are:
- Amplify Signals: Boosts weak control signals to power the motor.
- Provide Power: Delivers the right voltage and current to the motor.
- Protect Components: Prevents damage from voltage spikes or overloads.
Why You Can’t Skip It:
Servo motors often need more power than a microcontroller can supply. A driver bridges this gap safely.
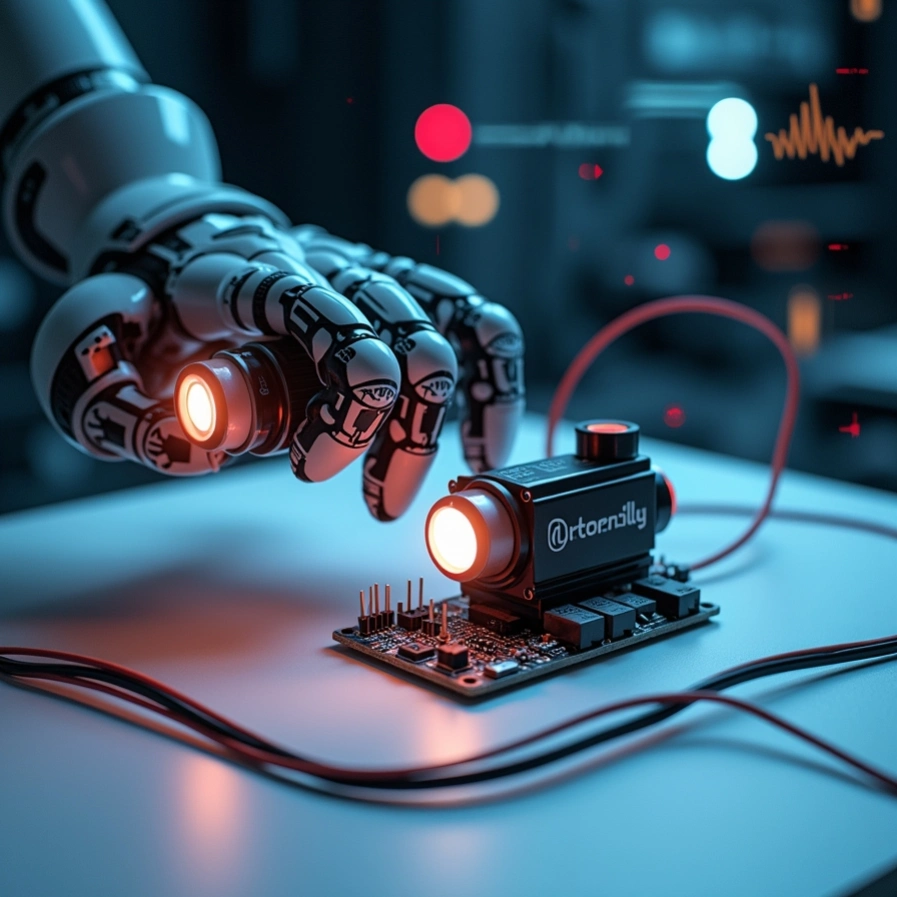
Types of Motor Drivers for Servo Motors
Not all drivers are the same! Here are the most common types:
1. PWM Motor Drivers
- How They Work: Send timed pulses to control the servo’s position.
- Best For: Basic hobby projects (e.g., Arduino robots).
- Example: PCA9685 PWM driver.
2. H-Bridge Drivers
- How They Work: Allow precise control of motor direction and speed.
- Best For: Advanced applications needing reverse motion.
- Example: L298N H-Bridge module.
3. Integrated Servo Controllers
- How They Work: Combine power delivery, signal processing, and safety features.
- Best For: Industrial systems (e.g., factory automation).
- Example: Pololu Maestro Servo Controller.
How to Choose the Right Motor Driver
Picking the perfect driver is like choosing shoes—you need the right fit! Here’s what to consider:
Factor | What to Check |
Voltage & Current | Match the driver’s specs to your servo’s needs. |
Compatibility | Ensure it works with your microcontroller (e.g., Arduino, Raspberry Pi). |
Size | Compact drivers for small projects; bulky ones for industrial setups. |
Safety Features | Overheat protection, surge resistance. |
Pro Tip: Always check your servo motor’s datasheet for voltage/current requirements!
Step-by-Step: Connecting a Motor Driver to a Servo
Let’s build a simple circuit using an Arduino and a PWM driver:
- Wire the Driver:
- Connect the driver’s power pins to a battery ( 6V).
- Link the driver’s signal pin to Arduino’s PWM pin ( Pin 9).
- Attach the Servo:
- Plug the servo’s three wires (power, ground, signal) into the driver.
Troubleshooting Common Issues
Problem: Servo jitters or doesn’t move.
- Fix: Check power supply—it might lack enough current.
Problem: Driver overheats.
- Fix: Add a heat sink or reduce load on the motor.
Problem: Servo moves erratically.
- Fix: Ensure wiring isn’t loose and signals aren’t interrupted.
Real-World Applications
Case Study 1:
A DIY enthusiast used a PCA9685 motor driver to control 16 servos in a robotic arm, enabling smooth, synchronized movements for picking up objects.
Case Study 2:
A factory upgraded to Pololu Maestro controllers for their packaging machines, cutting downtime by 30% thanks to precise motor control.
FAQs: Your Questions Answered
Q: Can I use any motor driver with my servo?
A: No! Always match voltage, current, and signal type (e.g., PWM).
Q: What happens if I pick the wrong driver?
A: The servo might underperform, overheat, or get damaged.
Q: Are motor drivers expensive?
A: Basic drivers cost5−20. Industrial-grade ones go up to $100+.
Q: Can I control multiple servos with one driver?
A: Yes! Multi-channel drivers (like PCA9685) handle up to 16 servos.
Conclusion: Power Up Your Projects!
A motor driver for servo motor is the secret sauce behind precise, reliable motion in automation. Whether you’re building a mini robot or optimizing a factory line, the right driver ensures your servo works smoothly and safely.
Next Steps:
- Grab a beginner-friendly driver like PCA9685 and start experimenting!
- Share your project in forums like Reddit’s r/robotics.
- Need help? Ask a mentor or watch YouTube tutorials.
About the Author:
John Carter is a robotics engineer with a decade of experience in automation. He’s passionate about making tech accessible to everyone—from pros to curious beginners.
сайт проституток